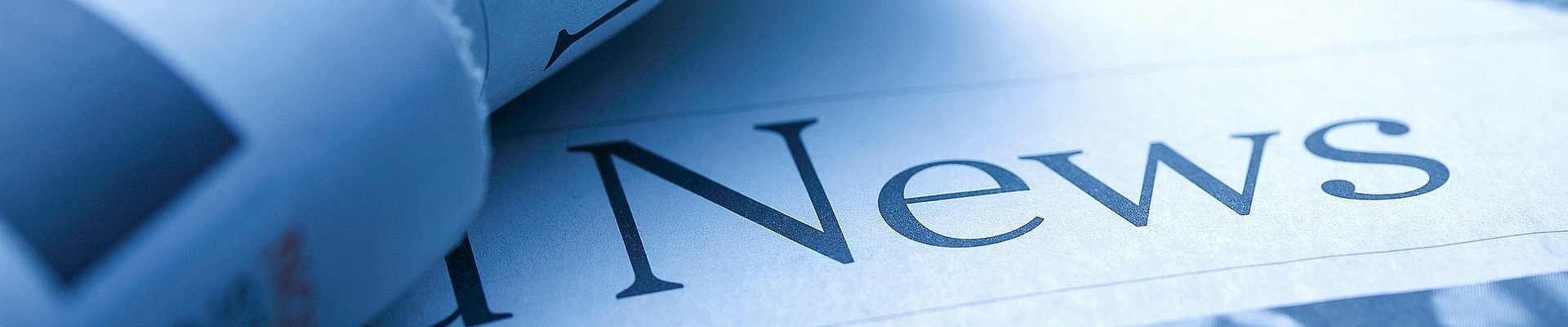
How to prevent corrosion and air holes in the die casting of security camera? What is the effect of high melting point?
Release time:
2023-01-10 13:52
author:
How to prevent corrosion and air holes in the die casting of security camera? What is the effect of high melting point? To understand.
How to prevent corrosion and air holes in the die casting of security camera? What is the effect of high melting point? To understand.
There are four main surface treatments to prevent the corrosion of the security camera die casting:
1. Electroplated die castings. This method is to put the security camera die-casting part into the metal solution, and then cover the surface of the standard part with a layer of metal through the current. This layer of metal has many functions. For example, we can use some different coating metals and choose some different coating metals. If we want to prevent the rust of die castings, we can galvanize the surface of standard parts.
2. For the surface of die-casting standard parts, some standard parts, such as drilling screws, require a hard surface, so the drilling screws can be heat treated to ensure that the drilling screws have sufficient hardness. This is the reason for heat treatment.
3. Mechanical electroplating of die-casting standard parts is to cold-weld metal particles onto the standard parts to ensure certain functions of the surface of the die-casting parts of the security camera. Mechanical plating and electroplating are basically similar, but we use different methods, and the results can be said to be the same.
4. For the surface passivation of the security camera die castings, the passivation mainly has two functions: one is to strengthen the hardness of the standard parts of the die castings, and the other is to greatly reduce the oxidation of the standard parts. In the process of surface treatment of die castings, we can choose the appropriate method according to the specific situation. In this way, die castings can play a better role in use.
The blowholes in the production of security camera die castings are caused by poor production, so how to prevent blowholes?
1、 Select the demoulding machine. A good demoulding machine will not produce gas and has better demoulding performance.
2、 The parameters of aluminum alloy die casting need to be adjusted. The filling speed should not be too fast to avoid air entrainment.
3、 In order to reduce the gas content in molten aluminum, the refining agent and degassing agent should timely clean the scum, bubbles and other oxides on the liquid surface.
4、 When the exhaust is not blocked, the mold must be kept smooth, and the exhaust must also be smooth.
5、 If the fastener has air holes, it is necessary to improve the mold and design.
6、 In the design of security camera die-casting products and molds, attention should be paid to core pulling and cooling to minimize excessive wall thickness difference.
What problems will be caused by the high melting point of the security camera die casting? Here is a brief introduction to its relevant knowledge points.
First, the high melting point of the security camera die casting will destroy the composition of the die casting. When magnesium and aluminum are lost due to temperature problems, the alloy composition will change, affecting the product quality, and the scrap rate will greatly increase.
The second is the high melting point of the security camera die casting, and the energy consumption cost will also increase. Generally, the solidification temperature of die casting in the production process is 410, and the poor may need to be set above 430. Generally speaking, every 10% increase in the temperature of the die-casting machine in the die-casting plant will increase the electricity charge by 5000 yuan per year. If diesel is used, the cost will increase by about 8000 yuan.
The third is the high melting point of the security camera die casting, which shortens the service life of the hot workpiece. If the temperature of the crucible is too high, it will accelerate the wear and corrosion of the hammer handle, gooseneck and crucible. This has led to many production problems, some of which may directly scrap equipment, greatly increasing costs.
Fourth, the increase of material melting point will cause great damage to the mold, reduce the service life of the mold, and increase the production cost.
Fifthly, the melting point of die casting mould is high, so the zinc slag produced will also increase, and the cost of effective alloy will greatly increase.
10
2023
-
01
How to polish the die casting of security camera
The appearance technology of the security camera die casting is rich, and the appearance effect of the security camera die casting is very beautiful. How to polish the security camera die-casting parts? Now let's have a look at the relevant content. I believe you can have a more detailed understanding.
04
2025
-
05
Unlocking the Potential of Brass Stamping Dies: A Comprehensive Guide
Brass stamping dies are essential tools in the manufacturing and machining sector, particularly in the production of metal components through stamping processes. These dies are specifically designed to shape and cut brass materials into precise forms, making them invaluable for various applications in industries such as automotive, electronics, and consumer goods. Understanding the significance of
03
2025
-
05
Unlocking Creativity: How Free Sample Brass Stamping Dies Can Transform Your Projects
Unlocking Creativity: How Free Sample Brass Stamping Dies Can Transform Your Projects Table of Contents 1. Introduction to Brass Stamping Dies 2. The Importance of Free Sample Brass Stamping Dies 3. How Brass Stamping Dies Work 4. Advantages of Using Brass Stamping Dies 4.1 Cost-Effectiveness 4.2 Precision and Quality 4.3 Versatility in Design 5. Applications of Brass Stamping Dies 5.1 Automotive