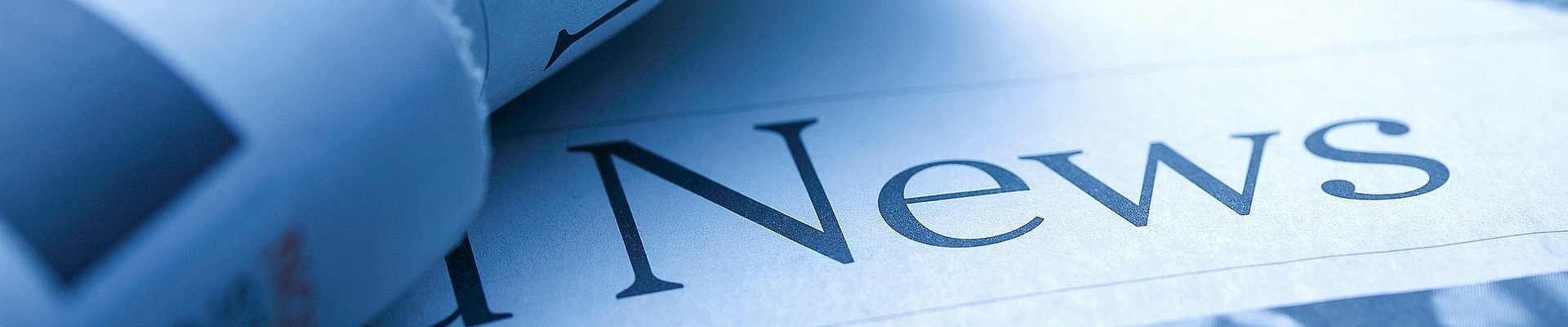
Understanding the Significance of OEM Prototype Plastic Molds in Modern Manufacturing Processes
Release time:
2025-07-10 10:00
author:
Understanding the Significance of OEM Prototype Plastic Molds in Modern Manufacturing Processes Table of Contents 1. Introduction to OEM Prototype Plastic Molds 2. What is OEM in Manufacturing? 3. The Importance of Prototype Plastic Molds 4. Key Benefits of Using OEM Prototype Plastic Molds 4.1 Cost Efficiency in Production 4.2 Enhanced Product Quality 4.3 Time-Saving Production Tech
Understanding the Significance of OEM Prototype Plastic Molds in Modern Manufacturing Processes
Table of Contents
- 1. Introduction to OEM Prototype Plastic Molds
- 2. What is OEM in Manufacturing?
- 3. The Importance of Prototype Plastic Molds
- 4. Key Benefits of Using OEM Prototype Plastic Molds
- 4.1 Cost Efficiency in Production
- 4.2 Enhanced Product Quality
- 4.3 Time-Saving Production Techniques
- 5. Applications of OEM Prototype Plastic Molds in Various Industries
- 6. The Design Process of OEM Prototype Plastic Molds
- 7. Challenges in OEM Mold Manufacturing
- 8. Future Trends in OEM Prototype Plastic Molds
- 9. Conclusion
- 10. Frequently Asked Questions (FAQs)
1. Introduction to OEM Prototype Plastic Molds
In today’s fast-paced manufacturing environment, understanding the role of **OEM (Original Equipment Manufacturer) prototype plastic molds** is essential. These molds serve as the backbone of various production processes, enabling manufacturers to create high-quality plastic products efficiently. By leveraging advanced technologies and innovative design strategies, OEM molds facilitate the production of complex shapes and components that meet specific customer requirements.
This article explores the multifaceted role of OEM prototype plastic molds in manufacturing, highlighting their **importance, benefits**, and applications across multiple industries.
2. What is OEM in Manufacturing?
OEM refers to companies that produce parts or products that are used in another company’s end products. In manufacturing, OEMs may create components or assemblies that are branded by another company. For instance, a manufacturer might design and produce a specific plastic component for a larger product that will be marketed under a different brand name. OEMs are crucial in maintaining **quality control** and **efficiency** throughout the production cycle, ensuring that products meet established standards and specifications.
3. The Importance of Prototype Plastic Molds
Prototype plastic molds are vital in the early stages of product development. They allow manufacturers to create tangible models of their designs, enabling testing and evaluation before full-scale production. This process not only validates the design but also provides insights into potential issues that could arise during manufacturing.
Moreover, prototype molds help in gathering feedback from stakeholders, which can be crucial for refining the final product. By utilizing these molds, companies can significantly reduce the risks associated with new product launches, saving both time and resources.
4. Key Benefits of Using OEM Prototype Plastic Molds
4.1 Cost Efficiency in Production
One of the most significant advantages of using OEM prototype plastic molds is the cost efficiency they offer. By identifying and resolving design flaws during the prototype phase, manufacturers can avoid costly revisions and delays during mass production. Additionally, the ability to produce smaller quantities of products for testing purposes reduces waste and helps manage production costs effectively.
4.2 Enhanced Product Quality
OEM prototype molds contribute to improved product quality. They allow for precise adjustments in designs based on extensive testing, ensuring that the final products are consistent and meet quality standards. This attention to detail not only enhances customer satisfaction but also strengthens a company’s reputation in the market.
4.3 Time-Saving Production Techniques
The use of OEM prototype molds streamlines the production process, significantly reducing the time required to bring a product to market. By identifying potential issues early on, manufacturers can refine their designs and develop more efficient production methods. This agility in the manufacturing process allows companies to respond swiftly to market demands and changes.
5. Applications of OEM Prototype Plastic Molds in Various Industries
OEM prototype plastic molds find applications across a wide range of industries, including:
- **Automotive Industry**: In automotive manufacturing, OEM molds are used to create intricate components such as dashboards, bumpers, and interior parts. These molds enable the production of lightweight yet durable plastic parts, contributing to overall vehicle performance and safety.
- **Consumer Electronics**: The consumer electronics sector relies heavily on OEM prototype molds for producing casings, buttons, and other components that require high precision and aesthetic appeal.
- **Medical Devices**: In the medical field, OEM molds are essential for creating devices that meet stringent regulatory requirements. These molds ensure that medical products are not only functional but also safe for use.
- **Packaging Solutions**: OEM molds are instrumental in the development of packaging materials. They allow manufacturers to create innovative and sustainable packaging that enhances product protection and shelf appeal.
- **Toys and Recreational Products**: The toy industry utilizes OEM molds to produce colorful and safe products that appeal to children. The ability to customize designs and create prototypes rapidly is particularly beneficial in this sector.
6. The Design Process of OEM Prototype Plastic Molds
The design process of OEM prototype plastic molds typically involves several key steps:
1. **Concept Development**: Initial ideas are brainstormed, focusing on the product's intended use and market requirements.
2. **CAD Modeling**: Computer-Aided Design (CAD) software is used to create detailed models of the product, allowing for visualization and adjustments before physical prototyping.
3. **Prototype Creation**: Using techniques such as 3D printing or CNC machining, the initial prototypes are produced for testing and evaluation.
4. **Testing and Validation**: Prototypes undergo rigorous testing to assess functionality, durability, and design effectiveness. Feedback is collected for further refinement.
5. **Final Design Adjustments**: Based on the testing results, necessary adjustments are made to the mold design to optimize performance and ensure quality.
6. **Production Preparation**: Once the design is finalized, the molds are prepared for mass production, and manufacturing processes are established.
7. Challenges in OEM Mold Manufacturing
Despite the many benefits, manufacturers face several challenges when using OEM prototype plastic molds:
- **Initial Cost Investment**: The upfront costs associated with creating high-quality molds can be substantial. Companies must weigh the long-term benefits against these initial expenditures.
- **Complexity of Designs**: As products become more complex, the molds required to produce them also become more intricate, leading to longer lead times and increased production difficulty.
- **Material Selection**: Choosing the right materials for mold production is critical. The materials must withstand the pressures of manufacturing while delivering the desired product quality.
- **Maintenance and Durability**: Molds require regular maintenance to ensure longevity and consistent performance. Manufacturers must develop strategies for upkeep to minimize downtime.
8. Future Trends in OEM Prototype Plastic Molds
The future of OEM prototype plastic molds is poised for transformation, driven by advancements in technology and changing market demands. Key trends include:
- **Increased Automation**: The integration of automation in mold production processes will enhance efficiency and precision, reducing labor costs and production times.
- **Sustainability Initiatives**: As consumers become more environmentally conscious, manufacturers will increasingly focus on creating sustainable products. This shift includes using eco-friendly materials and developing molds that minimize waste.
- **Advanced Materials**: The development of new materials, such as bio-based plastics and composites, will offer manufacturers more options for creating innovative products.
- **Digital Twins**: The concept of digital twins—virtual replicas of physical products—will allow manufacturers to simulate and test prototypes in a digital environment, further reducing costs and speeding up the design process.
9. Conclusion
OEM prototype plastic molds play an indispensable role in modern manufacturing. By facilitating the development of high-quality, precision-engineered products, these molds help companies achieve efficiency and adaptability in a competitive market. Understanding the importance, benefits, and applications of OEM molds is crucial for manufacturers aiming to enhance product quality while minimizing costs. As technology continues to evolve, the landscape of OEM prototype plastic molds will undoubtedly undergo significant changes, paving the way for a more innovative and sustainable future in manufacturing.
10. Frequently Asked Questions (FAQs)
What is the difference between OEM and ODM?
OEM (Original Equipment Manufacturer) refers to companies that produce components or products that are used in another company's end products. ODM (Original Design Manufacturer), on the other hand, designs and manufactures products that are then rebranded by another company.
How long does it take to produce OEM prototype plastic molds?
The production time for OEM prototype plastic molds can vary significantly based on complexity, design requirements, and the manufacturing process used. Typically, it can take anywhere from a few weeks to several months to complete.
Are OEM prototype molds customizable?
Yes, OEM prototype molds can be highly customized to meet specific design requirements and functionality needs. Manufacturers can make adjustments based on customer feedback and product testing.
What materials are commonly used for OEM prototype molds?
Common materials for OEM prototype molds include aluminum, steel, and various types of plastics. The choice of material depends on factors such as durability, cost, and the specific application of the mold.
How can businesses ensure the quality of their OEM prototype molds?
Businesses can ensure the quality of OEM prototype molds by selecting reputable manufacturers, conducting thorough testing during the prototype phase, and establishing clear quality control measures throughout the production process.
oem prototype plastic mold
10
2023
-
01
How to polish the die casting of security camera
The appearance technology of the security camera die casting is rich, and the appearance effect of the security camera die casting is very beautiful. How to polish the security camera die-casting parts? Now let's have a look at the relevant content. I believe you can have a more detailed understanding.
12
2025
-
07
Unlocking the Secrets of Wholesale Prototype Plastic Molds: A Comprehensive Guide
Unlocking the Secrets of Wholesale Prototype Plastic Molds Table of Contents 1. Introduction to Prototype Plastic Molds 2. The Importance of Wholesale Prototype Plastic Molds in Manufacturing 3. Types of Prototype Plastic Molds 3.1 Injection Molds 3.2 Blow Molds 3.3 Compression Molds 4. Benefits of Using Wholesale Prototyp
11
2025
-
07
Understanding Prototype Plastic Mold OEM: A Comprehensive Guide
The world of manufacturing, particularly in the domain of plastic molding, is rapidly evolving with the advent of advanced technologies and methodologies. One area that has gained considerable attention is "prototype plastic mold OEM" (Original Equipment Manufacturer). This term refers to the practice of creating prototype molds for plastic parts, tailored specifically to meet the unique requireme