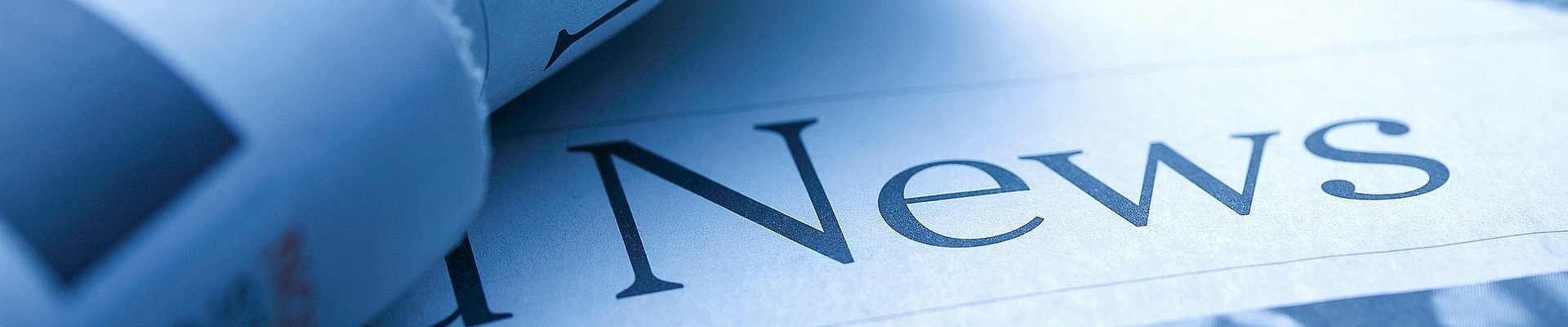
Unlocking Efficiency: The Advantages of Tailored Prototype Plastic Molds for Enhanced Production
Release time:
2025-07-08 10:40
author:
Unlocking Efficiency: The Advantages of Tailored Prototype Plastic Molds for Enhanced Production Table of Contents 1. Introduction to Customized Prototype Plastic Molds 2. Understanding Precision in Manufacturing 3. Key Benefits of Customized Prototype Plastic Molds 3.1 Cost-Effectiveness of Tailored Solutions 3.2 Enhanced Product Quality and Consistency 3.3 Time Effi
Unlocking Efficiency: The Advantages of Tailored Prototype Plastic Molds for Enhanced Production
Table of Contents
- 1. Introduction to Customized Prototype Plastic Molds
- 2. Understanding Precision in Manufacturing
- 3. Key Benefits of Customized Prototype Plastic Molds
- 3.1 Cost-Effectiveness of Tailored Solutions
- 3.2 Enhanced Product Quality and Consistency
- 3.3 Time Efficiency in Production
- 3.4 Design Flexibility and Innovation
- 4. The Prototyping Process for Customized Molds
- 4.1 Initial Consultation and Requirements Gathering
- 4.2 The Design Phase: From Concept to CAD
- 4.3 Testing and Modifications: Refining the Prototype
- 5. Case Studies: Success Stories of Customized Molds
- 6. Frequently Asked Questions About Customized Prototype Plastic Molds
- 7. Conclusion: The Future of Customized Production
1. Introduction to Customized Prototype Plastic Molds
In today’s competitive manufacturing landscape, the demand for efficiency, quality, and innovation drives businesses to seek advanced solutions that can meet their specific needs. Customized prototype plastic molds have emerged as a crucial component in achieving these goals. By tailoring the design and functionality of molds to match unique product requirements, companies can significantly enhance their production processes. This article delves into the multitude of benefits that customized molds bring to the table, along with insights into the prototyping process that ensures optimal results.
2. Understanding Precision in Manufacturing
Precision is the cornerstone of successful manufacturing. In industries that rely on plastic molding, the accuracy of molds directly impacts the quality and performance of the final product. Customized prototype plastic molds enable manufacturers to achieve precise dimensions, intricate designs, and consistent production standards. This level of precision is essential not only for meeting customer expectations but also for reducing waste and minimizing production costs.
3. Key Benefits of Customized Prototype Plastic Molds
3.1 Cost-Effectiveness of Tailored Solutions
Investing in customized prototype plastic molds can lead to significant cost savings over time. While the initial expenditure may be higher than standard molds, the long-term benefits often outweigh this upfront cost. Tailored molds reduce material waste, minimize production errors, and enhance efficiency. By producing parts that fit perfectly with minimal adjustments, companies can save on both labor and material costs, ultimately leading to a better return on investment.
3.2 Enhanced Product Quality and Consistency
One of the standout advantages of customized molds is the ability to produce high-quality, consistent products. Standard molds often result in variations that can affect the performance and aesthetics of the final items. Customized molds allow for strict adherence to design specifications, ensuring that each piece meets the required quality standards. This improvement not only enhances customer satisfaction but also builds a strong reputation for the manufacturer.
3.3 Time Efficiency in Production
Time is a critical factor in manufacturing. Customized prototype plastic molds can significantly reduce production time by streamlining the molding process. With molds designed specifically for the intended application, manufacturers can achieve faster cycle times and quicker changeovers. This efficiency allows companies to respond to market demands rapidly and efficiently, ultimately leading to increased profitability.
3.4 Design Flexibility and Innovation
The ability to innovate is vital in today’s fast-paced market. Customized molds provide the flexibility needed to explore new designs and materials. Manufacturers can experiment with different shapes, sizes, and functionalities without the constraints of standard molds. This adaptability not only fosters creativity but also enables businesses to stay ahead of the competition by offering unique and differentiated products.
4. The Prototyping Process for Customized Molds
Creating customized prototype molds involves a meticulous process designed to ensure the end product meets all specifications. This multi-step approach allows for comprehensive planning, testing, and refinement.
4.1 Initial Consultation and Requirements Gathering
The prototyping process begins with an initial consultation where manufacturers discuss their specific needs and expectations. This stage involves gathering information about the product, including dimensions, materials, and any unique features that should be incorporated into the mold. Open communication is essential as it lays the foundation for a successful project.
4.2 The Design Phase: From Concept to CAD
Once the requirements are established, the design phase commences. Utilizing advanced Computer-Aided Design (CAD) software, engineers create detailed digital models of the proposed mold. This stage allows for precise visualization and adjustments, ensuring that all specifications are met before the physical mold is produced.
4.3 Testing and Modifications: Refining the Prototype
After the CAD designs are finalized, a prototype mold is manufactured for testing. This mold undergoes rigorous trials to assess its performance and identify any necessary modifications. By analyzing the results, engineers can make adjustments to improve functionality and ensure that the final product aligns with the client’s expectations.
5. Case Studies: Success Stories of Customized Molds
To illustrate the effectiveness of customized prototype plastic molds, we can explore a few case studies from various industries:
- **Automotive Sector**: A leading automotive manufacturer faced challenges in producing a component that required precise dimensions for optimal performance. By investing in a customized mold, they reduced production defects by 30% and significantly improved assembly line efficiency.
- **Consumer Electronics**: A company specializing in consumer electronics required a unique casing for a new gadget. Utilizing customized molds allowed them to achieve intricate designs that enhanced the product’s aesthetics while maintaining structural integrity, leading to a successful product launch.
- **Medical Devices**: A healthcare manufacturer needed molds for delicate plastic components used in medical devices. Customized molds ensured the necessary precision and quality, resulting in products that met stringent regulatory standards and delivered reliable performance.
These cases highlight how customized molds can lead to measurable success in various sectors, resulting in improved product quality and operational efficiency.
6. Frequently Asked Questions About Customized Prototype Plastic Molds
What materials are typically used for customized plastic molds?
Customized plastic molds can be made from a variety of materials, including steel, aluminum, and various types of plastics. The choice depends on the specific requirements of the project, including durability, cost, and production volume.
How long does it take to produce a customized prototype mold?
The timeline for producing a customized prototype mold can vary depending on complexity and specifications. On average, the entire process can take anywhere from a few weeks to several months, including design, prototyping, and testing phases.
Can customized molds be reused for future projects?
Yes, one of the benefits of customized molds is their potential for reuse in future projects, especially if the same or similar parts are needed. This can lead to further cost savings in subsequent production runs.
Are customized molds more expensive than standard molds?
While the initial investment in customized molds may be higher, the long-term benefits often justify the cost. Customized molds help reduce material waste and ensure higher quality, leading to overall savings in production.
How do I know if customized molds are the right choice for my project?
Customized molds are ideal for projects that require specific designs, high precision, and consistent quality. If your project has unique requirements or high production volumes, investing in customized molds is likely a beneficial choice.
7. Conclusion: The Future of Customized Production
The advantages of utilizing customized prototype plastic molds are clear: from cost savings and improved product quality to enhanced innovation and efficiency. As the manufacturing industry continues to evolve, the role of tailored solutions becomes increasingly vital. Companies that embrace customized molds not only enhance their production capabilities but also position themselves as leaders in their respective fields. As we look to the future, investing in customized solutions will undoubtedly remain a key strategy for success in an ever-competitive market.
customized prototype plastic mold
10
2023
-
01
How to polish the die casting of security camera
The appearance technology of the security camera die casting is rich, and the appearance effect of the security camera die casting is very beautiful. How to polish the security camera die-casting parts? Now let's have a look at the relevant content. I believe you can have a more detailed understanding.
08
2025
-
07
Unlocking Efficiency: The Advantages of Tailored Prototype Plastic Molds for Enhanced Production
Unlocking Efficiency: The Advantages of Tailored Prototype Plastic Molds for Enhanced Production Table of Contents 1. Introduction to Customized Prototype Plastic Molds 2. Understanding Precision in Manufacturing 3. Key Benefits of Customized Prototype Plastic Molds 3.1 Cost-Effectiveness of Tailored Solutions 3.2 Enhanced Product Quality and Consistency 3.3 Time Effi
07
2025
-
07
Customizing Prototype Plastic Molds: A Comprehensive Guide
When it comes to manufacturing processes, prototype plastic mold customization is an essential step that allows businesses to bring their ideas to life with precision and efficiency. A prototype mold serves as a template for creating plastic parts and products, enabling manufacturers to test designs before committing to full-scale production. This process not only saves time but also reduces costs